DHL Supply Chain has partnered with Locus Robotics to improve picking productivity at its warehouse in Welham Green. Ursula O’Sullivan-Dale tours the facility to discover how the ‘bots are working their magic…
The pandemic has accelerated the booming trend of e-commerce, making the labour-intensive picking process in e-fulfilment play an even bigger and more critical role in meeting high end-customers’ demands. In turn, these trends have speeded up the introduction of new technologies in various industries, but especially in warehousing.
And the round-the-clock order processing site for British retailer Marks & Spencer in Welham Green, Hatfield, operated by contract logistics provider DHL Supply Chain, is a great example of how robotic automation can increase efficiency and accelerate delivery processes. The impressive facility boasts a footprint totalling one million square feet and can stock three million single items at once – or 86km (53.4km) worth of stock, the same distance as a drive between central London and Oxford.
To help run this mammoth operation, DHL has enlisted the help of Locus Robotics, which has deployed a fleet of its signature autonomous mobile robots (AMRs), dubbed LocusBots, at the fulfilment site to help with the one of the most strenuous and time-consuming manual tasks in a warehouse: picking. Simon Woodward, head of accelerated digitalisation and innovation, UK and Ireland at DHL Supply Chain, explains that the partnership came about after DHL saw the LocusBots in action at a couple of US sites.
“Locus, at that time, was only operating in the USA,” he says. “The company was keen to work with DHL because it saw it as an opportunity to get into other regions. We were obviously keen to work with them because we’d seen the technology work in the US, so it’s very mutually beneficial… the partnership built from there and I think it’s something that will continue growing as Locus expands its range of robots as well.”
The assisted picking robots, which were originally trialled at Welham Green pre-lockdown in early 2020, now total 92 units across the entire site and have been working side by side with human colleagues for 18 months. What’s more, Welham Green was the first site in the UK to deploy the LocusBots, with another following suit after their picking success, which includes a 40% increase in productivity on the ground floor and 25% growth on another floor.
A friendly face
The staff work in close collaboration with the robots, with Woodward emphasising that the machines represent a form of assistance, rather than a replacement, for human workers. The robots work in a three-to-one formation, with three bots to every one employee on the warehouse floor. At the start of a shift, after employees have been briefed, the bots kick off the day’s operations by heading to a location to begin picking. Locations are precisely mapped, with specific labels for bays where items are stored helping the bots find the exact items they need. The bots then autonomously head to a bay to begin a pick and wait for a human worker to join them.
Pointing to the importance of robot-human teamwork, Woodward says: “The collaborative nature of the bots is very important. The upskilling of colleagues to understand what the system does, but also the new opportunities that this type of system gives to colleagues for their development and for their future careers, is important.”
Walking through the warehouse floors, the LocusBots whizz past with empty totes or successful picks, with the robot determining whether to complete one or two picks in a single run based on the weight of its current payload.
According to Woodward, staff attitudes have been pretty open towards the bots. “After the initial pilot, colleagues could just see the logic of doing it that way. They could see the changes from their previous role being much more physical, strenuously pushing trolleys and changing it for the better. With anything like this there’s always that question of ‘are robots going to replace our jobs?’ But once you’ve communicated and explained how this works, that there’s still a role for people and that it’s very much a collaborative system, the robots are just seen as part of the furniture.”
To help integrate the bots, the Welham Green site also launched a mini competition that asked staff to come up with names for the robots. The prize? A mini bot model of their very own.
In terms of accuracy, the robots support the workers by automating most of the picking process for them. Workers are responsible for the quantity of items that go inside the cart, while the robots calculate how many items are needed, the type and where they are located. They are also responsible for carrying the successful picks around the site, saving vital time and energy for the employees.
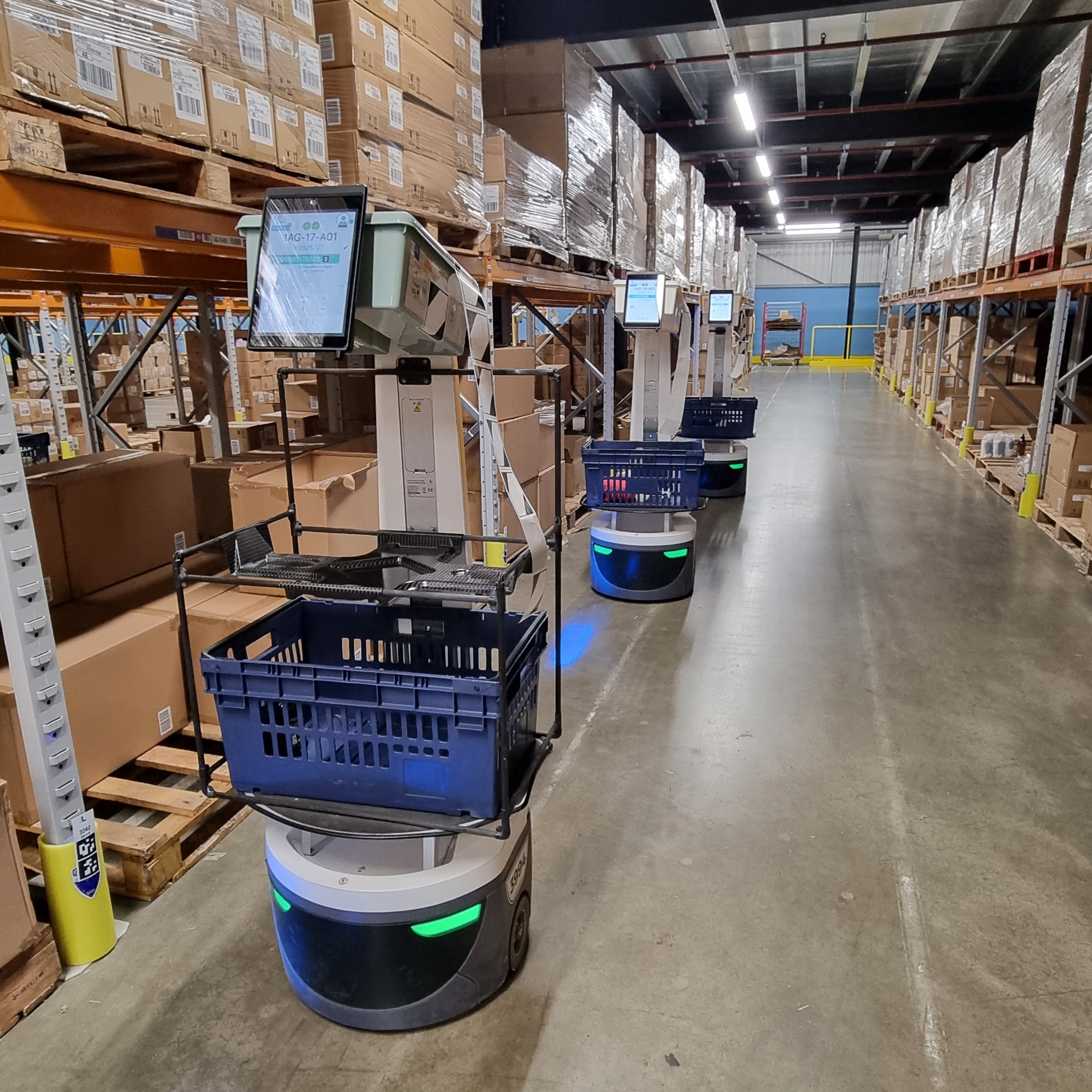
Pointing to the reliability of the machines, Woodward says, “As long as they’re well-maintained and all the sensors are regularly cleaned, then the bots will maintain their accuracy. They always go where they’ve been told to go, that’s never been an issue.” And as with normal staff, peak periods mean the site has a need for more workers, with DHL negotiating with Locus to bring more bots in on a contractual basis.
Data digging
However, though the machines’ chief purpose is picking assistance, the LocusBots aren’t just a bit of extra muscle. Rather, they offer a range of software and data-driven advantages for the warehouse team. As Woodward points out, “Locus helps us to optimise the picking a lot better than trying to do it manually. There’s an initial sort of productivity improvement that partly comes from that better optimisation.
“But the knock-on effect is the amount of data that a first line manager gets on the shop floor from looking at the control screens; that’s live, and you can see where the bots are, therefore you can direct your workforce and know where to look for them and where your people are. You can see that visually, but then there’s a whole suite of KPIs as well. You can see your overall productivity in 15-minute time slices, and you can look ahead and see if it is going to be a busy day.
“Using the Locus system, we can say with confidence when we’re going to finish. That’s because it’s getting that real-time data from the system that says in these 15 minutes we’ve done 100 picks or lines per hour, and if we keep going at that rate then we know we’ll make it by a certain time. That data provides a different dimension to how our colleagues manage. It makes it initially more complicated but, once you’ve explained to staff how to use that data, it allows them to do their jobs better.”
With all this data, there are certainly challenges. However, there are also opportunities, with Woodward explaining some of the training and upskilling benefits that come from the LocusBots, as well as DHL’s wider shift to digital-led processes. “It can lead to roles in data analytics, and we’ve got apprenticeships at various levels at the moment. We’re looking to expand on the back of that area, and not just on the back of Locus, but for all the other types of systems that we deploy as well. Existing employees take the vast majority of those opportunities.
“It might be anything from a Level 3 apprenticeship where they start to learn about Excel and how to programme and not just do the basics of Excel, but take it to the next level. Then you get involved in how to present that data using different software platforms and Python programming and analytics and the value of data science. There’s lots of productivity in that area, so we can take our colleagues on that journey at the same time as bringing the systems in that will give us all this data. We’ve got to make sure we don’t just have all that data and do nothing with it.”
Hurdles to overcome
Though the LocusBots appear to have made life easier around the warehouse, implementing the new robotic workforce wasn’t all plain sailing. Specifically, Woodward points to the difficulties involved in IT integration and the complexity of the system.
“The IT integration was a big thing because the bots basically get a wave of orders, so at the start of the day our warehouse management system will send to the Locus system all the orders. As every location is individually numbered, every item you’re picking has an individual SKU. All that information must be transferred across to Locus and then they’ve got to have a virtual map of the whole picking area and know where all the locations are.
“So, you need to get that whole setup working and the orders to be transferred seamlessly in the IT world over to their system. Then, when Locus does its thing and a colleague performs a pick, a confirmation is sent back to our warehouse management system. Getting that right and making sure it was fully tested and working smoothly was key.”
Any change, highly technical or not, can be overwhelming and Woodward explains that speaking to employees is integral to any successful shift in operations. The other most significant hurdle for the bots was that implementation meant, according to Woodward, “changing people’s processes”. He says: “Whenever you do that, it starts with communicating to colleagues, making sure they understand what it is that’s changing and explaining that really clearly to them.” Once the employees were on board with the bots and the collaborative nature of the process was made clear and understood, the bots were free to work their magic and help speed up the picking process throughout the site.
For DHL and the Welham Green facility, the LocusBots have shown, and continue to show, the value of automated solutions for the modern warehouse. Woodward also sees robotics as part of an ongoing vision for the future of DHL’s logistical operations. “Robotics are definitely part of it, whether it’s one supplier or another, that will evolve over time. But in terms of how we want to deploy robotics and digitalisation, it’s only going in one direction and that’s to do as much of it as we can.” END
Pick and mix
DHL’s Welham Green site is full of automated solutions that assist the picking and transportation of goods throughout the warehouse. These include an automated clothes rail provided by Dürkopp Fördertechnik, a logistics technology firm and subsidiary of Knapp Group, plus automated barcode scanners, labelling solutions and more. The LocusBots are just the latest in a long line of technologies designed to make the warehouse more efficient but have quickly become a key part of its successful operation.
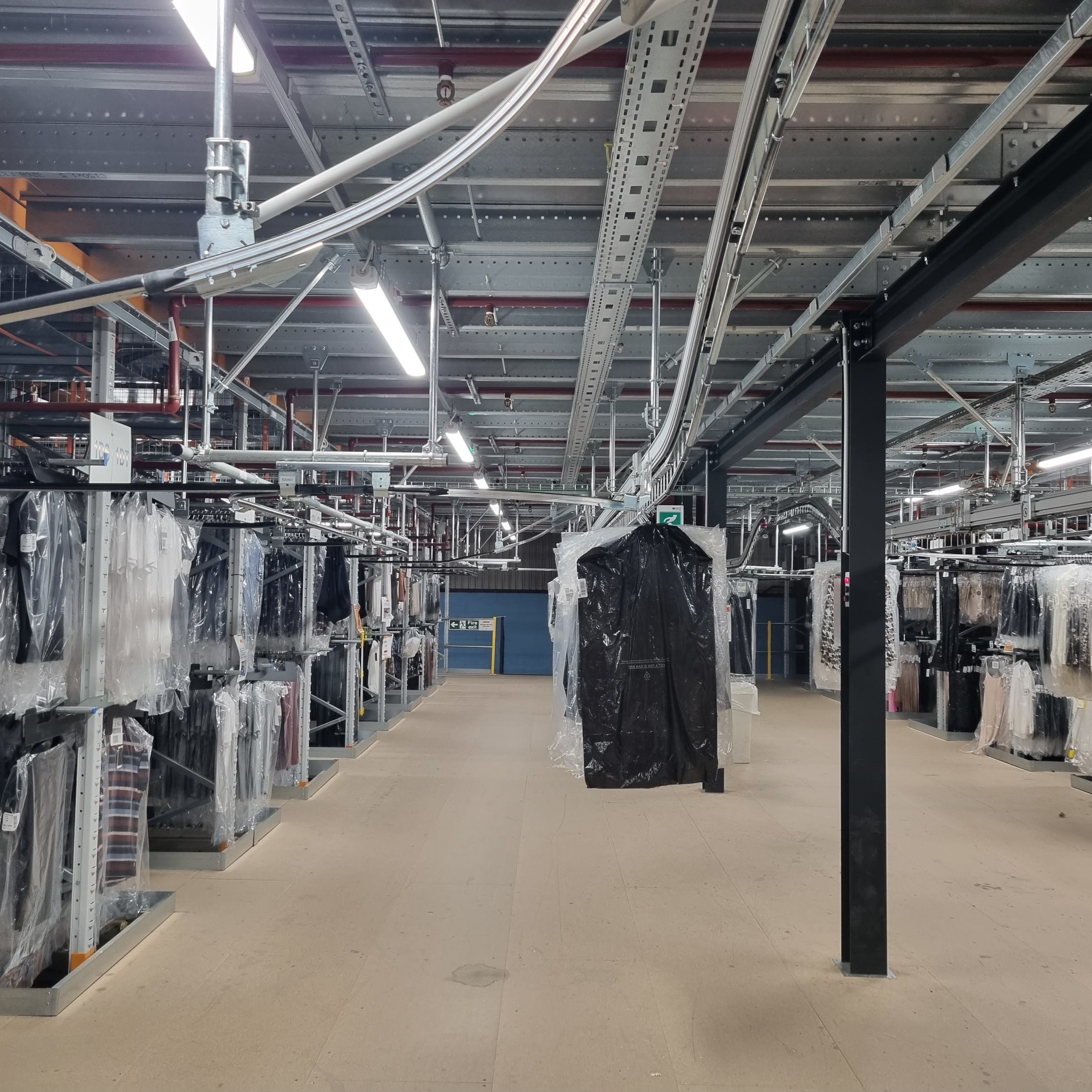
On the first floor of the warehouse, hanging rails are used by staff for manual picking. Items are packed onto racks that are hooked onto the mechanical rail for scanning and dispatch. The rail is fitted with scanners that pick up on the type of product being moved and where it is supposed to be transported, including information such as the name of the destination store. Other key tech includes barcode scanners, which automate the scanning of dolly labels attached to totes leaving the warehouse, thus replacing the manual scanning process. This automated system is, according to Rodney Rajack, operations manager at the Welham Green site, “five times faster and much more accurate than its manual equivalent”.
One in a billion
In September, Locus Robotics announced its AMRs had surpassed one billion units picked. The achievement was made at a major home improvement retailer warehouse in Florida, USA and was reportedly attained just 59 days after Locus registered 900 million units picked, underscoring the ever-increasing high order processing volume taking place. For contrast, it took Locus 1,542 days to pick its first 100 million units.
This article was originally published in the October 2022 issue of Robotics & Innovation. Read the original article.